Variations in the internal structure of mobile LH2 transport trailers significantly affect boil-off gas production. By optimizing tank geometry, you can reduce heat transfer and minimize structural stress, which in turn decreases boil-off. Utilizing effective insulation and efficient cooling systems will help maintain low temperatures, further mitigating gas loss. Proper pressure management is essential for safety and efficiency. There's much more to discover about design choices that influence boil-off in transport trailers.
Key Takeaways
- Variations in internal cooling systems can significantly affect temperature maintenance and thus influence boil-off gas production in mobile LH2 transport trailers.
- The geometric design of internal structures, such as baffles, can optimize heat transfer efficiency and minimize boil-off gas generation during transport.
- Different materials used in the internal structure, particularly those with lower thermal conductivity, can reduce heat influx and lower boil-off levels.
- Effective pressure management systems within the trailer can help control boil-off gas by maintaining optimal pressure during loading and unloading operations.
- High-performance insulation materials integrated into the trailer's internal structure are crucial for minimizing heat transfer and reducing overall boil-off gas.
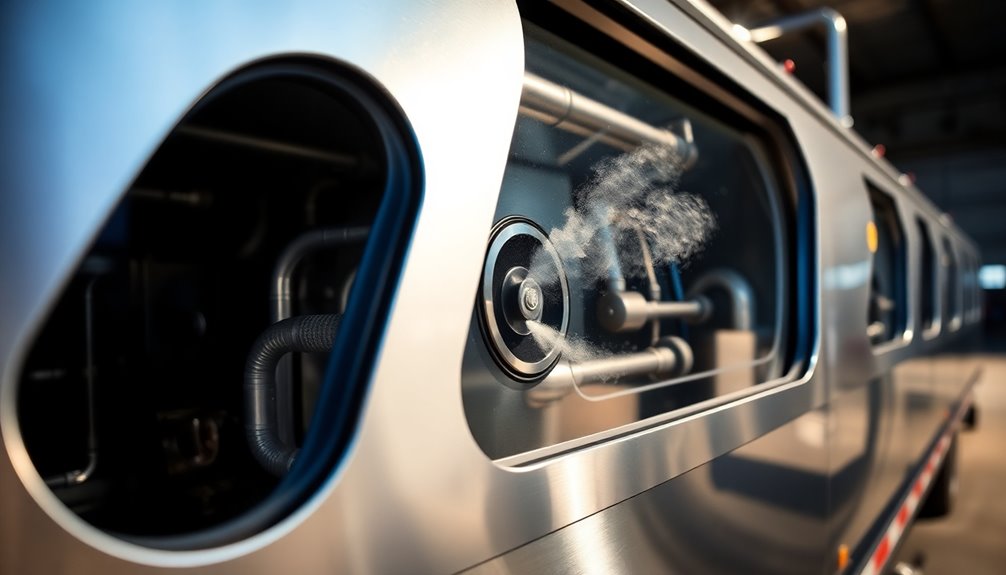
As you explore the impact of internal structure on boil-off gas, you'll find that material properties and tank design play crucial roles in heat management. The thermal conductivity of materials, such as aluminum and stainless steel, directly influences how heat transfers within the tank. Aluminum, with its higher conductivity, can facilitate faster heat transfer, potentially increasing boil-off gas production. Choosing materials with lower thermal conductivity and optimizing insulation effectiveness are vital for minimizing heat influx and reducing boil-off gas. Additionally, hydrogen's role as a critical energy carrier makes it essential to manage boil-off gas effectively in transport applications.
Tank design and configuration also significantly affect boil-off gas dynamics. Incorporating internal cooling systems can help maintain low temperatures, while optimizing tank shape and size reduces heat transfer and structural stress. Specialized designs like zero boil-off tanks aim to maintain optimal conditions, effectively eliminating boil-off gas. The geometry of cylindrical versus spherical tanks impacts heat transfer efficiency and structural advantages, so selecting the right shape can be critical.
Tank design and configuration are vital for managing boil-off gas, with specialized shapes and internal cooling systems playing crucial roles.
Pressure management systems are essential in controlling boil-off gas. Efficient pressure transfer mechanisms and pressure control valves help minimize boil-off during loading and unloading. Maintaining the maximum allowable working pressure is important for safety; however, if not managed correctly, it can also increase the risk of boil-off gas. Controlled venting systems allow for pressure management while minimizing losses, and continuous pressure monitoring ensures optimal conditions.
Understanding heat transfer dynamics is key to reducing boil-off gas. Minimizing heat influx paths from ambient conditions and utilizing high-performance insulation materials can significantly lower heat transfer. Active cooling systems can maintain low temperatures, reducing the likelihood of gas production during transport. Managing thermal expansion is equally important, as it helps prevent structural damage and excessive boil-off.
Finally, operational practices and adherence to safety codes are crucial. Efficient loading and unloading procedures, compliance with safety standards, and regular risk assessments contribute to minimizing boil-off during transport. By maintaining optimal operating temperatures and having emergency protocols in place, you can further reduce the risks associated with boil-off gas.
Frequently Asked Questions
What Materials Are Used in the Construction of LH2 Transport Trailers?
When constructing LH2 transport trailers, you'll find a combination of high-quality materials.
Stainless steel forms the outer framework due to its durability, while high-strength aluminum alloys contribute to a lighter structure.
Vacuum super insulation minimizes heat transfer, and aluminum shields reflect radiation.
Composite materials enhance strength-to-weight ratios, and cryogenic compatible materials handle extreme temperatures.
These selections ensure safety and efficiency for transporting liquid hydrogen effectively.
How Is Boil-Off Gas Measured in These Trailers?
You measure boil-off gas in trailers using a combination of thermodynamic models, real-time data collection systems, and experimental measurements.
Sensors track temperature, pressure, and volume changes, providing critical insights into the boil-off rates, often expressed in kg/hr.
By analyzing flow rates and implementing top fill techniques, you can minimize losses.
Real-time analytics help you assess these losses immediately, enabling you to take action and enhance delivery efficiency during operations.
What Safety Measures Are Implemented for LH2 Transport?
When you're dealing with liquid hydrogen, it's like juggling fireballs while blindfolded!
You've got to wear flame-resistant clothing, face shields, and clean insulated gloves. Keep at least 10 meters from flammable materials and ensure proper ventilation.
No cell phones allowed, and you need trained personnel for transport. Regular maintenance is a must, while fencing keeps out the curious.
Safety isn't just a suggestion; it's essential for keeping everyone safe and sound!
Are There Regulations Governing Mobile LH2 Transport Trailers?
Yes, there are regulations governing mobile LH2 transport trailers.
You'll find that these trailers must comply with U.S. Department of Transportation regulations and receive safety certifications from relevant bodies, like the Korean Gas Safety (KGS).
They also need to adhere to specific safety standards, including hazard management, spill containment measures, and operational requirements for emergency controls.
Ensuring compliance helps maintain safety for personnel and the environment during LH2 transport operations.
What Are the Environmental Impacts of Boil-Off Gas?
Imagine a balloon slowly deflating, releasing a potent gas with every breath.
That's what happens with boil-off gas (BOG). If you don't manage it well, it contributes to increased greenhouse gas emissions, especially methane.
You'll find that proper strategies can transform BOG into a resource rather than a waste. By using it as fuel, you integrate its emissions into your total footprint, making compliance with environmental regulations not just necessary, but beneficial.
Conclusion
In conclusion, understanding how variations in internal structure affect boil-off gas from mobile LH2 transport trailers is crucial for optimizing efficiency and safety. You might wonder, what if these insights could lead to significant cost savings and enhanced performance? By addressing these structural factors, we can reduce gas loss and improve the reliability of hydrogen transport. Embracing these changes will not only benefit the industry but also pave the way for a more sustainable future.